MASONRY: Case Study: Wet-Polisher Makes Sculpting Four Tons of Granite Smooth
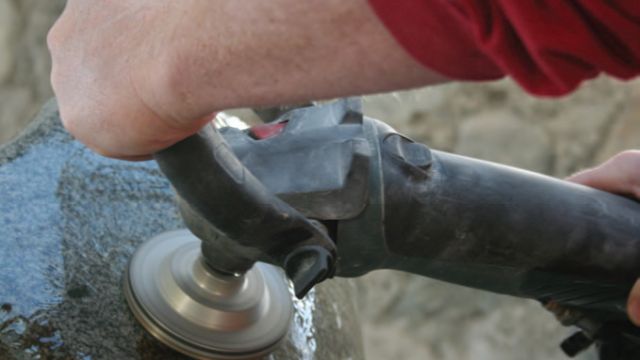
Imagine a four-ton piece of granite in front of you. To some it may seem like a barrier, an obstacle to overcome. To others, it is merely a piece of stone, or a slice of heaven waiting to be cut into. David Sywalski, an artist who works with the LaFollette Design Group in Cherryfield, Maine, sees this piece of granite as a canvas with which he can create art.
For more than 20 years Sywalski has studied and worked as an artist with a focus on sculpting. Over the years, he has worked on many projects utilizing various materials including metal and stone to create everything from larger-than-life sculptures to jewelry. A recent project took him to Maine Quarry in Chandler Bay, Maine, and had him working with granite that historically has been used for many architectural applications. It also is known for its great working qualities including the way it splits, carves, chisels and polishes.
Granite is an aesthetically pleasing material, once it has been polished. However, because it is such a durable stone, it can be extremely hard on the tools that are being used on it.
“The particular piece of granite I sculpted is medium grained with an even medium brown color. It is both beautiful and resilient,” says Sywalski. “I also incorporated a piece of Heritage Valley granite from J.C. Stone Inc. into this sculpture that weighed approximately five tons. This too is a sturdy piece of stone. My tools need to be able to withstand the stress I put them under.”
GETTING STARTED
Because of his numerous years of experience, Sywalski knew that very few tools are tough enough to work on granite. “In the stone working industry, angle grinders are considered disposable tools because of the harshness of the working conditions,” said Sywalski. “I needed to find various tools that were resilient enough to withstand this enormous job and perform as I need them to.”
As a result of the type of sculpting Sywalski was doing, he needed a variety of tools to perform different jobs, including an impact hammer that could split the stone off of the quarry block; a heavy-duty angle grinder that could be used vertically, horizontally and in all different odd angles for rough carving and large removal of stone; a variable speed angle grinder that could provide a more fine-tuned removal of material; and a wet polisher that could finish the stone and show its true beauty.
FINDING THE RIGHT TOOL TO FINISH THE JOB
Over the years Sywalski had used a variety of tools by various manufacturers to sculpt and polish pieces of art work purchased by art collectors from all over the United States. “Based on my experience,” he says, “I knew for this particular project that, when it came time to finish and polish the stone I was sculpting, I needed a tool that would not only be durable but also extremely efficient. I wanted a tool that had a center water feed for polishing and grinding and a core drill. I also wanted a tool that would cut down on my polishing time.”
After working with tools marketed by well-known manufacturers and various other pneumatic makes, Sywalski decided to try a wet polisher on the market that featured the center water feed he was looking for along with diamond polishing pads, snail lock carbide bricks, diamond cup wheels that were extra coarse and a diamond core drilling bit.
“Out of all the tools in my toolbox, this by far was the tool I used most on this project,” he says. “I used the cup wheels and carbide stones to perform final shaping of the sculpture and the diamond pads for polishing. If you keep proper stone and wheel contact and grind in the sweet spot, this machine out performs all others on the market today, including the so called ‘standard’ of the industry.”
CUTTING WORK TIME IN HALF
“Polishing and finishing with Metabo’s PWE11-100 wet polisher has cut my polishing time by more than half. I was able to use five-inch diamond pads instead of three-inch pads,” says Sywalski. “I was also able to remove material for long periods of time without overworking the machine. The machine’s cooling system works so well, I could feel it cooling down in my hand as I held it.”
The versatile wet polisher designed for polishing also works well for grinding when a cup wheel is used. “I was impressed with the tool’s core drilling capability. I was able to core drill 14-inch holes at sizes at 3⁄4-inch, one inch and 1.5 inches. Core drilling is very sensitive to machine speed. The wet polisher enabled me to find the correct speed for each core bit. I was able to core drill 11 two-inch-diameter holes at 30 seconds an inch in some of the hardest granite found in the industry.”
A VALUABLE TOOL IN A STONE CARVER’S STUDIO
Upon completion, the sculpture weighed about seven tons and was proudly displayed at the Coastal Maine Botanical Gardens. “It is nice to work on a project and have all the tools that I originally started the job with to complete the job,” says Sywalski.
Originally published in Masonry magazine.
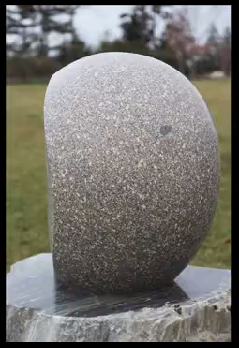
ABOUT THE AUTHOR
Masonry, the official publication of the Mason Contractors Association of America, covers every aspect of the mason contractor profession - equipment and techniques, building codes and standards, business planning, promoting your business, legal issues and more. Read or subscribe to Masonry magazine at www.masonrymagazine.com.